What Kind of Printer Do I Need to Make Shirts at Home?
What Kind of Printer Do I Need to Make Shirts at Home?
4 Answers
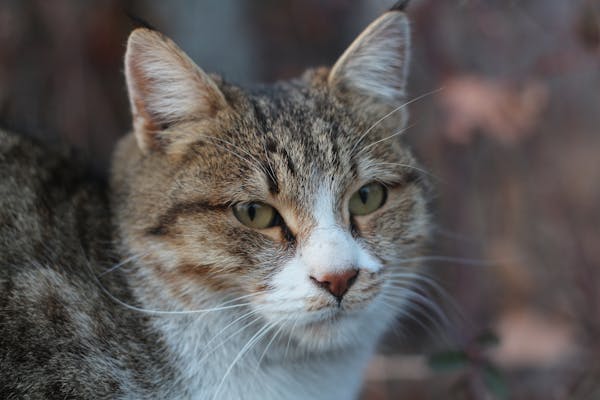
When it comes to printing shirts, the type of printer you choose plays a huge role in the overall process. Whether you’re diving into a business or just having fun with custom designs, picking the right printer is key. Here’s a straightforward guide to help you out.
The custom T-shirt market has blown up recently. Thanks to new tech, there are loads of ways to print shirts these days. From DTG printers to heat transfer printers, each comes with its own perks and downsides. Knowing what each one does can help you decide what’s right for your shirt-making needs.
Here are the most common types of printers used for T-shirt printing:
- Direct-to-Garment (DTG) Printers
- These printers are made for fabric printing, perfect for small to medium runs. They use water-based inks, which are eco-friendly. DTG printers can handle multiple colors at once, which is great for intricate designs.
- Pros: High-quality, full-color prints; can use various fabrics like cotton and blends; easy to use.
- Cons: Can be pricey; limited print area; may need special ink and maintenance.
- Screen Printing Presses
- This traditional method uses a stencil and ink to transfer a design onto the shirt, ideal for bulk production with solid colors.
- Pros: Cost-effective for large orders; vibrant, long-lasting prints; works with many fabric types.
- Cons: Time-consuming setup; needs a separate screen for each color; not great for small or multi-color runs.
- Inkjet Printers
- Popular for T-shirt printing due to affordability and versatility, using CMYK inks for a wide range of colors.
- Pros: Affordable; can print on various fabrics; high-quality, vibrant prints; user-friendly.
- Cons: Prints may not be as durable; can clog or smudge; frequent ink replacements needed.
- Laser Printers
- Laser printers use a laser to create an image on a drum that attracts toner particles. Though not as common, they print high-quality images quickly.
- Pros: Crisp text and images; fast; works with various papers.
- Cons: Limited fabric compatibility; expensive; not great for large quantities.
- Dye-Sublimation Printers
- These use heat to transfer dye onto fabric, creating permanent, full-color images, mainly on polyester and synthetics.
- Pros: High-quality prints; works on various synthetics; long-lasting.
- Cons: Not compatible with natural fibers; expensive; needs special paper.
- Heat Transfer Printers
- Designs are printed on transfer paper and then applied to fabric with heat. Can use inkjet or laser printers based on the transfer paper.
- Pros: Affordable for small to medium runs; minimal equipment needed.
- Cons: Quality and durability vary; additional steps might be needed.
- Direct-to-Film (DTF) Printers
- DTF is a newer method where a design is printed on film and then transferred to fabric using heat.
- Pros: Flexible with many fabrics; vibrant, durable designs; no fabric pre-processing needed.
- Cons: Being new, fewer options available; might need extra equipment for heat transfer.
- Vinyl Heat Transfer
- Involves cutting out designs from vinyl sheets and applying them with heat. It’s simple but needs a vinyl cutter.
- Pros: Great for logos and text; durable.
- Cons: Single-color designs only; additional cutting equipment needed.
Picking the right printer depends on your specific needs. Think about:
- Volume of Production
- For small orders, DTG printers are popular since they handle small batches well. Screen printing works better for large batches due to its cost-effectiveness.
- Design Complexity
- DTG printers are the go-to for complex, colorful designs. Screen printing or heat transfer might work for simpler graphics.
- Fabric Type
- DTG printers are great for cotton and blends, dye-sublimation for polyester, and screen printing works with most fabrics.
- Budget
- Printer costs vary. DTG printers ($2,000-$5,000) are on the higher end. Heat transfer and inkjet printers start around $500, while screen printing presses, especially automated ones, can be quite the investment.
- Print Quality and Durability
- If high quality and durability are must-haves, DTG and dye-sublimation are top picks. Screen printing also delivers lasting results with the right inks.
- Ease of Use and Maintenance
- For beginners, DTG and heat transfer printers are simpler to handle. Screen printing requires more setup and know-how.
- Special Requirements
- Consider any specific needs, like printing on dark shirts or needing to churn out a certain number in a set time.
Here are some recommended printers:
- Epson SureColor F570
- A high-end dye-sublimation printer for polyester and other synthetics, producing vibrant, durable prints.
- Brother GTX
- A DTG printer perfect for directly printing on garments, offering high-quality prints and user-friendly operation.
- HP DesignJet Z9+
- A versatile inkjet printer for various fabrics, providing excellent print quality, ideal for high-res prints.
- Riley Hopkins 300
- An automated screen printing press for small to medium batches, known for its speed and ease of use.
- MECOL 650DHT DTF Printer
- Great for DTF printing, offering vibrant prints on different films and perfect for businesses entering DTF printing.
- Mecolour A234 Sublimation Printer
- Excellent for sublimation printing on polyester fabrics, designed for high-volume production.
- Canon PIXMA Pro-100
- An affordable inkjet for heat transfer printing, known for its great color accuracy, suitable for detailed designs on cotton.
- Brother HL-L8360CDW
- A laser printer with sharp text and color reproduction, ideal for simple designs on dark shirts using laser transfer paper.
Picking the right printer doesn’t have to be daunting. Consider your production needs, design complexity, fabric type, and budget. Whether you’re starting a business or just having fun designing shirts, there’s a printer out there that’s just right for you. Happy printing!
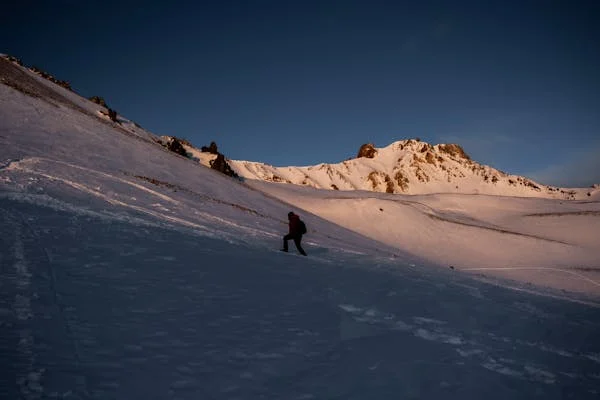
So, you want to make custom shirts? Well, the type of printer you’ll need kinda depends on the printing method you’re diving into. Let’s break down the main options and what they require:
Inkjet Printers for Heat Transfer Printing
Alright, if you’re going the inkjet route for heat transfer printing, here’s what you need to know. The deal is, you print your design on special transfer paper, then use a heat press to get it onto the shirt. When picking an inkjet printer, you might want to look out for:
- Can it handle heat transfer paper made for inkjets? Make sure of that.
- You gotta get the print quality right—high DPI settings are your friend for vibrant prints. Personally, I’ve heard folks rave about the Epson EcoTank ET-3850 for its killer image quality and cost-effective inks.
- Cost matters, right? Some printers have those high-capacity ink tanks, letting you print a ton before hitting the cartridge store. The EcoTank series is big on this.
Sublimation Printers
Now, if it’s all about flashy, full-color designs on polyester shirts, sublimation printers are your jam. These printers work with sublimation ink and special paper. Here’s the scoop:
- These printers dig polyester—shoot for at least 60% in the fabric, but 100% is the dream.
- Either grab a dye-sublimation printer like the Epson SureColor F170, or get your hands on an inkjet and convert it (but note, converting might void warranties).
- You definitely need a heat press to lock in those designs.
Direct-to-Garment (DTG) Printers
If it’s high-quality prints on cotton you’re after, DTG printers are the move. Think of them like souped-up inkjets made just for clothes. Here’s what’s up:
- DTG prints offer sick detail and colors with decent speed. Models like the G4 are pretty impressive for that.
- They rock with natural fibers like cotton but can be meh on synthetics compared to sublimation.
- Heads up: These tend to be pricier, but the quality and versatility could be worth it.
Laser Printers
Not as popular as others but some folks do use laser printers for heat transfer. Here’s what to watch for:
- Can the printer handle heat transfer paper without sweating bullets?
- Laser prints are solid and long-lasting but might not pop like inkjet or sublimation prints on fabric.
To wrap it up, if you’re gearing up for shirt-making, your go-to printer totally depends on print quality, fabric, and your cash stash. Just so you know:
- Lots of designs across different fabrics? Inkjet printer with heat transfers could be your best bet.
- Into poly shirts with vibrant vibes? A sublimation printer is your buddy.
- Cotton shirts with straight-up awesome prints? DTG printers have got your back.
Honestly, what it boils down to is picking the right method and printer based on what you want to see hanging in your closet.
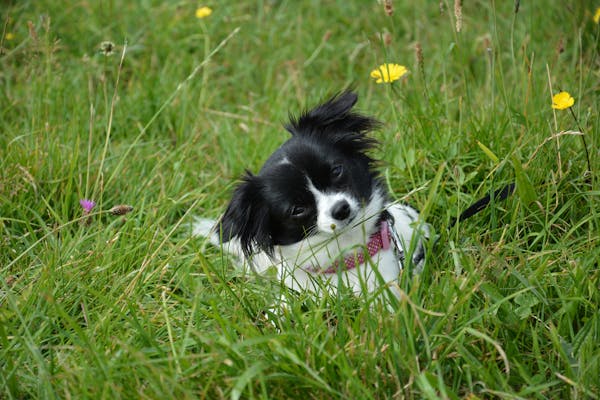
Looking to print your own custom shirts? There are a few things to consider when choosing the right printer, like the type of fabric you’re using, how detailed your design is, your budget, and how big of a production you’re planning. Here’s the scoop on different printers and what they’re best for, so you can figure out what suits you.
- Inkjet Printers (Tweaked for Transfers)
- What they do: These bad boys print your design on transfer paper, which you can then heat-press onto the fabric.
- Perfect for: If you’re just doing a few pieces, dabbling in the craft, or need unique designs for gifts.
- Upside: Cheap to start—most folks have an old inkjet lying around. Good with both cotton and polyester mixes.
- Downside: Sometimes the transfers can crack over time. Not as durable as direct fabric printing.
- How it’s done:
- Print your mirrored design on sublimation or heat-transfer paper.
- Use a heat press (ideal settings: 380°F for 15–30 seconds) to transfer the print.
- Direct-to-Garment (DTG) Printers
- How it works: These printers lay the ink straight onto the fabric using special water-based inks.
- Aces for: Cotton tees with intricate, colorful designs in small to medium numbers.
- Pros: High detail and super soft prints. Skip those annoying setup fees or making screens.
- Cons: Upfront costs can bite—sometimes over $100k. Dark fabrics need a bit of pretreatment.
- Brands to watch: Epson F2100 and Brother GTX are big names here.
- Screen Printing
- Not exactly a printer but kind of related: Good old stencils (screens) apply ink in neat layers.
- Top choice for: Large runs and bold designs using fewer colors.
- Pros: Costs way less per shirt when you’re making loads. Super durable, vibrant results.
- Cons: Not the best for small orders or complex artworks. Needs time for setup and drying.
- Dye-Sublimation Printers
- What it does: Transfers ink using heat from sublimation paper onto polyester fabrics.
- Who it’s for: If you’re working with polyester or polymer-coated fabrics like sportswear.
- Positives: Colors pop and don’t fade easily. The print becomes one with the fabric.
- Negatives: Sticks to white or light-colored polyester only. Needs a heat press and the right paper.
- Direct-to-Film (DTF) Printers
- How it operates: Prints onto PET film, which is then transferred to fabric with adhesive and heat.
- Best for: Different fabrics (cotton, polyester), detailed designs, and small to medium batches.
- Pros: No fabric prep needed. Handles both dark and light fabrics efficiently.
- Cons: Feels a bit stiffer than DTG prints. You’ll need a bit of extra gear—a curing oven or heat press.
- Choosing the Right Printer
- Fabric Compatibility: Cotton goes well with DTG or screen printing. Polyester thrives under sublimation or DTF.
- Budget: Going lean: Inkjet for transfers or basic DTF (~$2k). Bit more spendy: Mid-range DTF or pre-owned DTG (~$15k). Big bucks: Industrial-grade DTG or full-throttle sublimation setups.
- Design Complexity: Multiple color gradients look great with DTG or DTF. Simpler logos shine with screen printing or inkjet transfers.
- Durability: Sublimation and screen printing can last through 50+ washes. DTG and DTF require proper curing to hit 30–50 washes.
- Common Challenges & Fixes
- Problem: Ink Cracking or Fading
- Why it happens: Low-grade transfers or uneven curing.
- What to do: For transfers: Use top-notch sublimation ink and apply even pressure with your heat press. For DTG/DTF: Cure prints at 320°F for about 1–2 minutes.
- Problem: Color Bleeding on Fabric
- What’s up: Wrong ink choice or fabric treatment issues.
- Solution: Cotton shirts need pretreating before DTG is applied. Choose polyester-specific sublimation ink for synthetic materials.
- Problem: Startup Costs are Sky-High
- Cause: Industrial equipment comes with a hefty price tag.
- Fix: Consider renting gear initially. Partner up with print-on-demand services for testing.
- Problem: Ink Cracking or Fading
- Recommended Setups
- DIY/Hobbyist: Modified inkjet printer with a heat press (~$800). Entry-level DTF printer, think A4 DTF machine.
- Small Business: Mid-range DTG or DTF printer with a heat press.
- Large-Scale Operation: Go big with industrial DTG or automated screen printing.
- Tips from the Trenches
- Test fabrics and inks before jumping into bulk printing.
- Give printers regular TLC—clean those DTG nozzles weekly.
- Blend different methods occasionally—use DTF for dark fabrics with sublimation for polyester.
Honestly, aligning that printer choice with your fabric, budget, and production scale will have you cranking out top-notch designs in no time.
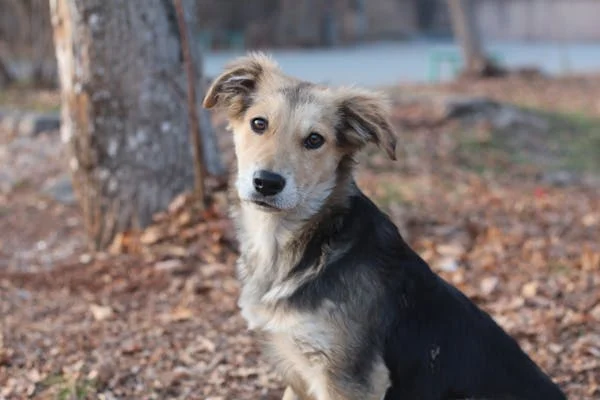
So, you want to dive into the world of shirt-making, huh? Picking the right printer can be a bit of a maze, but don’t sweat it too much! It’s all about the printing method you fancy. Let’s break down some solid choices for you.
Inkjet Printers
These bad boys are pretty flexible and often the go-to for heat transfer stuff. Grab yourself some of that special transfer paper, print your design, and let a heat press do its magic on the fabric. If sublimation printing sounds like your jam, just swap out the regular ink for sublimation ink, and you’re good to go, especially if you’re working with polyester.
Laser Printers
Laser printers can team up with heat transfer paper too. Once you’ve got your design on the paper, apply it with a heat press for designs that are crisp and stand the test of time. This method is quick and can save you some bucks, which is never a bad thing.
Dedicated Sublimation Printers
If you’re after some vibrant, super-durable prints, sublimation printers are the real MVP. They churn out designs using sublimation ink that you transfer onto polyester fabric, perfect for detailed and colorful artistry.
Direct-to-Garment (DTG) Printers
DTG printers are like the magic wand for fabric. They print straight onto shirts without needing any transfer paper. Perfect for detailed works with loads of colors on various materials. You’ll feel like a wizard creating those high-quality masterpieces!
Key Things to Keep in Mind:
- Fabric Type: For sublimation, polyester is your best buddy; for heat transfer, you’ve got more wiggle room with fabrics.
- Quality of Prints: Make sure your printer can dish out high resolution and true-to-life hues.
- The Budget: Inkjet printers? They’re usually easier on the wallet. But if you’re leaning towards sublime sublimation or DTG, be ready to shell out a bit more dough.
If you’re still scratching your head, there are a bunch of resources out there, like TechRadar’s guide on the best T-shirt printers for 2024, and Printify can steer you in the right direction too. Trust me, a little research goes a long way!